Junjie Chen 1*
1, Department of Energy and Power Engineering, School of Mechanical and Power Engineering, Henan Polytechnic University, Henan, China
E-mail:
cjjtpj@163.com
Received: 03/02/2022
Acceptance: 19/02/2022
Available Online: 20/02/2022
Published: 01/07/2022

Manuscript link
http://dx.doi.org/10.30493/DAS.2022.327865
Abstract
The increasing popularity of carbon nanotubes has created a demand for a fundamental understanding of thermal transport characteristics in nanostructured materials. However, the effects of impurities, misalignments, and structure factors on the thermal conductivity of carbon nanotube films and fibers are still poorly understood. In this article, carbon nanotube films and fibers were produced, and the thermal conductivity was determined using the parallel thermal conductance technique. The effects of carbon nanotube structure, purity, and alignment on the heat conduction properties were investigated to understand thermal transport characteristics in the nanostructured material. The importance of bulk density and cross-sectional area was determined experimentally. The results indicated that the prepared carbon nanotube films and fibers are highly efficient at conducting heat. The structure, purity, and alignment of carbon nanotubes played a fundamentally important role in determining the heat conduction properties of carbon films and fibers. Single-walled carbon nanotube films and fibers had higher thermal conductivity, while the presence of non-carbonaceous impurities degraded the thermal performance due to the low degree of bundle contact. The thermal conductivity may present power law dependence with temperature. The specific thermal conductivity decreased with increasing bulk density. A maximum specific thermal conductivity was obtained at room temperature, but Umklapp scattering occurred. The fibers have better specific thermal conductivity properties than the films due to the increased degree of bundle alignment.
Keywords: Carbon nanomaterial, Carbon fibers, Thermal properties, Thermal conductivity, Umklapp scattering
Introduction
Carbon nanotubes can exhibit a unique ability to conduct heat [1][2], referred to as heat conduction properties. A thermal barrier is formed in the radial direction and it was reported that thermal conductivity of an individual single-walled carbon nanotube is around 1.52 W/(m·K) in the radial direction at room temperature [3]. In contrast, the thermal conductivity in the longitudinal direction is around 3500 W/(m·K) at room temperature [4]. Therefore, carbon nanotubes show superior heat conduction properties along the longitude directions. Consequently, carbon nanotubes outperform diamond as the best thermal conductor. When macroscopic, ordered assemblies are formed, the thermal conductivity could reach up to around 1500 W/(m·K) at room temperature [5]. The heat conduction properties of carbon nanotube networks vary significantly, with a minimum of thermal conductivity less than 0.1 W/(m·K) [6]. The heat conduction properties depend on a variety of factors such as impurities and misalignments. Single-walled carbon nanotube are stable up to around 1000 K in air and around 3000 K in vacuum [7]. The study of heat transport phenomena involved in carbon nanotubes is an active area of interest [8] due to the potential for applications in thermal management.
Carbon nanotubes have unique thermal properties, potentially making this nanostructured material useful in thermal management applications such as nanofluids. Traditional fluids play an important role in many industry fields, but their inherently low thermal conductivity seriously hampers the development of energy-efficient heat transfer fluids. However, the heat conduction properties can be improved significantly by dispersing nanoparticles, such as carbon nanotubes, in fluids [9][10]. Dispersion can be achieved by physical and chemical treatments. Fluids containing nanoparticles present substantial advantages over traditional fluids in terms of thermal conductivity and heat-transfer capability [11][12]. The thermal conductivity can be substantially increased, which is crucial in applications with high heat-transfer capability demand [13][14]. For example, nanofluids in solar collectors is an important application [15][16] in which nanofluids are employed for their tunable optical properties [17][18]. Nanoparticles of various materials have been used to produce nanofluids, such as titania, copper, aluminum, copper oxide, aluminum oxide, and carbon nanotubes. Of these nanoparticles, carbon nanotubes hold the greatest promise due to their unique heat conduction properties.
The thermal conductivity of carbon nanotubes depends heavily upon crystallographic defects. Phonons can scatter due to crystallographic defects leading to an increased relaxation rate, thereby decreasing thermal conductivity associated with the reduced mean free path of phonons [19][20]. In single-walled carbon nanotubes, the mean free path varies from 50 nm to 1500 nm [21][22]. Crystallographic defects will lead to a significant reduction in the mean free path [23], for example, 4 nm or less [24]. The thermal conductivity of carbon nanotubes also depends upon the structure of the nanotubes. The thermal conductivity of multi-walled carbon nanotubes is significantly higher than the sum of each shell due to the inter-wall interactions [25]. With an identical diameter configuration, single-walled carbon nanotubes have better heat conduction properties [26] due to an increase in cross-sectional area.
Bulk carbon nanotubes can be used as composite fibers in polymers [27][28], but the bulk structure will reduce the ability to conduct heat, causing a decrease in thermal conductivity [29][30]. The thermal conductivity of carbon nanotube fibers is comparable to that of common metals [31]. However, through chemical modification, the ability to conduct heat is comparable to or higher than that of highly conductive metals such as copper [32]. The thermal conductivity varies significantly depending upon the density and cross-sectional area of the bulk material. The bulk carbon nanotube material contains pores [33][34]. Consequently, the thermal conductivity of the non-compact bulk material is much lower than that of the skeletal material [35][36] since the bulk volume is inclusive of the void fraction. The skeletal portion of the bulk material is often referred to as the “matrix” or “frame” [37, 38]. However, there is considerable uncertainty in the determination of the density of the bulk material [39][40]. Consequently, the effects of carbon nanotube structure, purity, and alignment on the thermal conductivity of carbon films and fibers are still poorly understood. Little research has been conducted to determine which parameters are important for high thermal conductivity.
This study relates to the heat conduction properties of carbon nanotube films and fibers. Carbon nanotube films and fibers were produced, and the thermal conductivity was measured using a steady-state method. The effects of carbon nanotube structure, purity, and alignment on the thermal conductivity were investigated to understand the characteristics of thermal transport in the nanostructured material. The objective is to gain insight into the fundamental characteristics of thermal transport in carbon nanotubes. Particular emphasis is placed on the dependence of thermal conductivity on carbon nanotube structure, purity, and alignment, with an attempt to improve the heat conduction properties for carbon nanotube films and fibers.
Experimental methods
Preparation of films and fibers
Carbon nanotube films were produced by spinning continuously onto a single rotational winder of a spinning machine. The preparation process of carbon nanotube films is depicted schematically in (Fig 1). A dense film was laid down with aligned carbon nanotube bundles. The dense film was sprayed with acetone to condense the carbon nanotube networks further. The carbon nanotubes were highly aligned by preparing a dense film in such a manner [41], although the surface tension effect is significant in the extrusion process [42]. A laser was used to cut the carbon nanotube film into small pieces to measure thermal conductivity. Carbon nanotube fibers were produced by stretching the dense film with two rotational winders of the spinning machine. The two rotational winders operate with only a small difference in rotation rate.
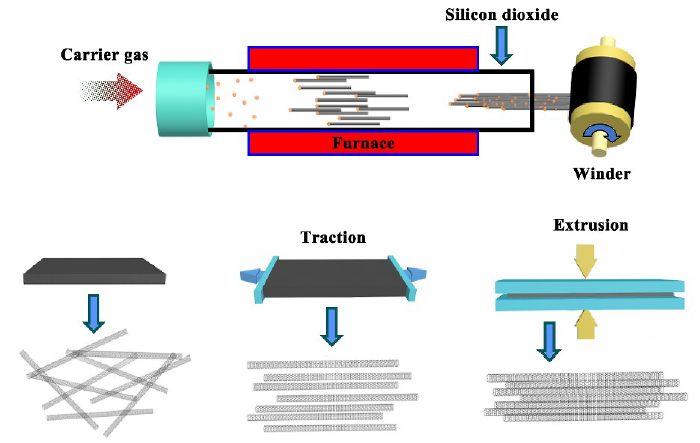
Material characterization
The prepared carbon nanotube fibers’ characterizations and surface morphology were determined using scanning electron microscopy (SU3800, Hitachi High-Tech Corporation).
Thermal conductivity measurement methods
Since the diameter of the needle-like samples was extremely small, the parallel thermal conductance technique [43][44] was employed to determine the thermal conductivity. Fourier’s Law was used to compute the thermal conductivity. This steady-state method has been carried out to measure the thermal conductivity of boron nitride nanotube sheets [45], carbon nanotube sheets [46], and yarns [47][48]. The configuration of the measurement system is depicted schematically in (Fig. 2). A preliminary measurement was performed with respect to the sample holder itself so as to determine the background or baseline heat conduction and losses. The sample was attached, and the thermal conductance was measured. In this method, all conductance factors arising from the system are accounted for. The radiative heat losses were caused primarily by the thermal radiation from the hot surface of the heater. However, such heat losses were already included in the baseline. Therefore, a correction factor of 0.5 was introduced into the method [43][44] to account for the radiative heat losses.
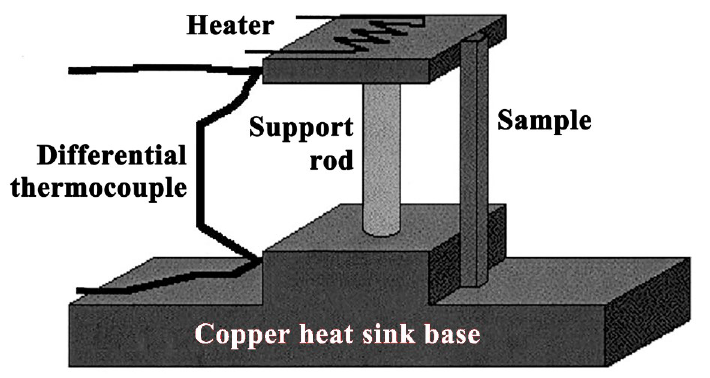
Linear mass density measurement methods
The linear mass density of the carbon nanotube films was measured using a gravimetric method [49]. On the other hand, the linear mass density of the carbon nanotube fibers was measured using a vibroscope method [49][50]. The fundamental frequency was measured. The specific thermal conductivity is defined as the thermal conductivity normalized by bulk density. The bulk density can be determined in terms of the linear mass density and the cross-sectional area.
Results and discussion
Material characterization
The carbon nanotubes showed highly alliance. However, the fiber material contains a relatively small amount of short, deformed carbon nanotubes. The carbon nanotubes are of the order of several hundred microns (Fig. 3).
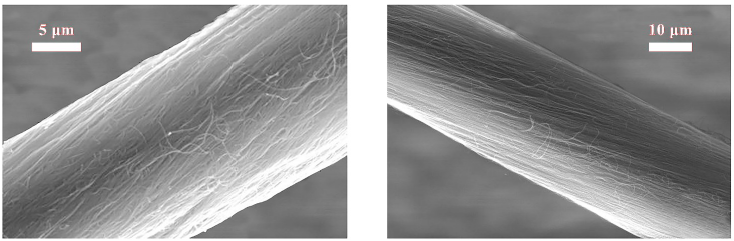
Four samples are prepared with different structures, purity, and alignment. Three structural parameters are selected in terms of alignment, purity, and the number of walls (Fig. 4). For type A, the carbon nanotube films or fibers are composed mostly of multi-walled carbon nanotubes. In addition, there is a small amount of short deformed carbon nanotubes. For type B, a mixture of carbon nanotubes is used. Specifically, the carbon nanotube films or fibers are composed of single-walled and multi-walled carbon nanotubes. In addition, there is a small amount of amorphous carbon. For type C, the carbon nanotube films or fibers are composed mostly of single-walled carbon nanotubes. In addition, there is a small amount of non-carbonaceous impurities. For type D, the carbon nanotube films or fibers are composed of single-walled carbon nanotubes with high purity. Understanding which parameters are important for high thermal conductivity is made possible by comparing heat conduction properties between the nanostructured materials.
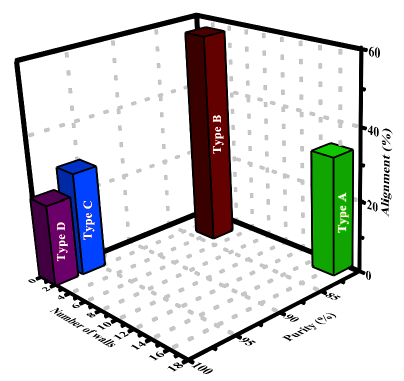
Thermal conductivity of films
The effects of structure, purity, and alignment on the specific conductivity of carbon nanotube films are illustrated in (Fig. 5 A) at different temperatures. The specific conductivity of the A-type film was lower than that of the other tested film types. Multi-walled carbon nanotubes generally have low thermal conductivity. Therefore, the specific conductivity A-type film was lower compared to films composed of single-walled carbon nanotubes. The specific conductivity of the D-type was higher than other tested film types. This superiority is due to the lack of non-carbonaceous impurities, which reduce the degree of bundle contact between single-walled carbon nanotubes and degrade the thermal performance of the C-type film. It is noted that specific thermal conductivity increased with the increase of test temperature in all types; however, the differences between the studied types in terms of specific conductivity also increased. For instance, the specific conductivity of D-type film at around 210 K was similar to that of A-type at 300 K. These results further highlight the importance of structure and purity in enhancing specific conductivity, especially at higher temperatures.
The effect of temperature on thermal conductivity for the carbon nanotube films is illustrated in (Fig. 5 B). The power law index was 1.87, 0.99, 1.80, and 1.96 for the thermal conductivity of the A, B, C, and D type films, respectively. Therefore, the thermal conductivity of all films presents power law dependence with temperature except for that of the B-type. The small value in B-type refers to a reduction in the propagation of phonons dimensionality [51][52] due to an increase in the degree of bundle alignment and contact. On the other hand, the power law index was the largest, although the small degree of bundle alignment, which reduces the mechanical stiffness of the film
The effect of bulk density on the specific thermal conductivity of the tested carbon nanotube films at room temperature is illustrated in (Fig. 5 C). The highest specific conductivity was achieved in D-type film. The lowest specific conductivity was obtained for the A-type film. A tentative explanation could be made for the distinctive phenomenon as the specific thermal conductivity decreases by increasing bulk density. The low bulk density of the D-type film compensates for the adverse effect of poor alignment on specific thermal conductivity. Therefore, the bulk density may be controlled to produce carbon nanotube films with high thermal conductivity.
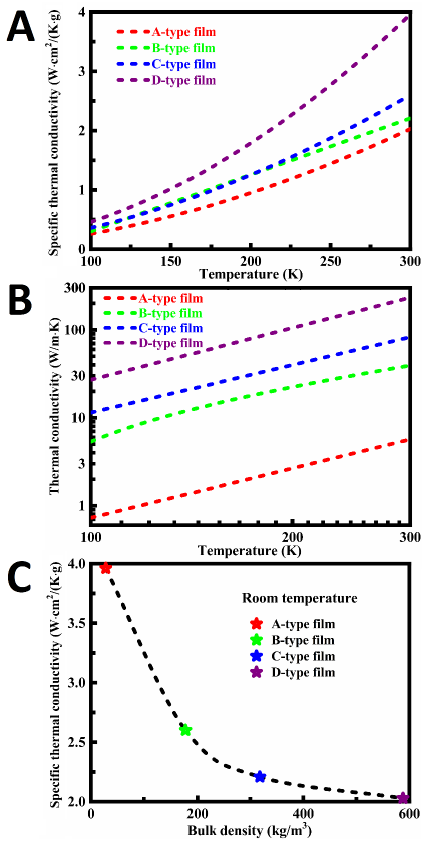
Thermal conductivity of fibers
The specific conductivity of the tested fibers was around 10 W·cm2/(K·g) at room temperature (Fig. 6 A), which is comparable to or higher than that of pristine and chemically modified carbon nanotube fibers [31][ 32]. A maximum specific thermal conductivity was obtained at room temperature, which corresponds with previous reports [32][52]. The maximum specific thermal conductivity represented by the peaks indicates the onset of Umklapp scattering. The Umklapp scattering is the dominant thermal resistivity process, limiting the specific thermal conductivity. The high thermal conductivity of carbon fibers is often associated with a high modulus of elasticity [53][54]. Therefore, the carbon nanotube fibers have sufficient strength to be used as a reinforcement for composite materials. The specific conductivity of the fibers was higher than that of the films. This increase is caused by the improved degree of bundle alignment for the fibers. A high degree of bundle alignment will lead to an increase in thermal conductivity due to the increased interfacial area between the carbon nanotubes.
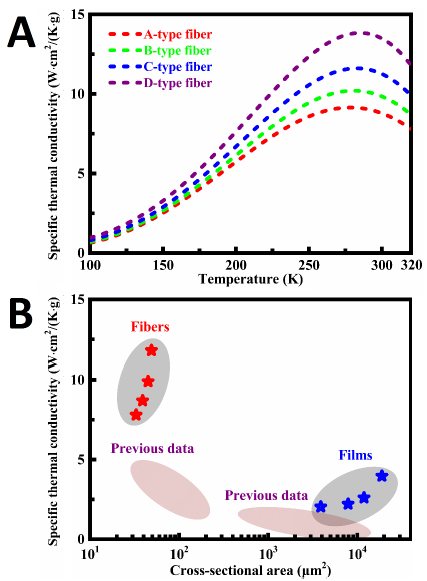
The effect of cross-sectional area on the specific thermal conductivity for the carbon nanotube films and fibers at room temperature is illustrated in (Fig 6 B). Previous data was also included for comparison [32][47][48][55-58]. Under the same cross-sectional area conditions, the specific conductivities of the films and fibers were higher than those previously reported in the literature. The carbon nanotubes were of the order of several hundred microns, which is significantly greater than the phonon mean free path. As the length of carbon nanotubes increases, the effect of temperature on thermal conductivity becomes more pronounced [4][58]. The length of the carbon nanotubes contained in tested films and fibers was much greater than that of previous reports. Consequently, the current films and fibers were highly efficient at conducting heat and typically have a higher specific thermal conductivity in comparison to the previous data.
Conclusions
Carbon nanotube films and fibers were produced, and the thermal conductivity was measured using a steady-state method. The effects of carbon nanotube structure, purity, and alignment on the heat conduction properties of carbon films and fibers were investigated to understand thermal transport characteristics in the nanostructured material. The major conclusions are summarized as follows:
- Multi-walled carbon nanotube films and fibers generally have low thermal conductivity.
- The presence of non-carbonaceous impurities reduces the degree of bundle contact between carbon nanotubes, increasing thermal resistance at the interface junctions and degrading thermal performance.
- The thermal conductivity presents power law dependence with temperature or has a linear relationship with temperature.
- The specific thermal conductivity decreases with increasing bulk density. Low bulk density can compensate for the adverse effect of poor alignment on specific thermal conductivity.
- A maximum specific thermal conductivity is obtained at room temperature because of Umklapp scattering.
- The specific thermal conductivity of the fibers is significantly higher than that of the films. The improved thermal properties are caused by the increased degree of bundle alignment.
- The prepared carbon nanotube films and fibers efficiently conduct heat due to the higher length factor.
References
1 | Ebbesen TW. Carbon nanotubes. Phys. Today. 1996;49(6):26-32. DOI |
2 | Ando Y, Zhao X, Sugai T, Kumar M. Growing carbon nanotubes. Mater. Today. 2004;7(10):22-9. DOI |
3 | Ibrahim KS. Carbon nanotubes-properties and applications: A review. Carbon Lett. 2013;14(3):131-44. DOI |
4 | Pop E, Mann D, Wang Q, Goodson K, Dai H. Thermal conductance of an individual single-wall carbon nanotube above room temperature. Nano Lett. 2006;6(1):96-100. DOI |
5 | Koziol KK, Janas D, Brown E, Hao L. Thermal properties of continuously spun carbon nanotube fibres. Physica E. 2017;88:104-8. DOI |
6 | Kumanek B, Janas D. Thermal conductivity of carbon nanotube networks: A review. J. Mater. Sci. 2019;54(10):7397-427. DOI |
7 | Thostenson ET, Li C, Chou TW. Nanocomposites in context. Compos. Sci. Technol. 2005;65(3-4):491-516. DOI |
8 | Rathinavel S, Priyadharshini K, Panda D. A review on carbon nanotube: An overview of synthesis, properties, functionalization, characterization, and the application. Mater. Sci. Eng. B. 2021;268:115095. DOI |
9 | Chand R, Rana G C, Hussein AK. On the onset of thermal instability in a low Prandtl number nanofluid layer in a porous medium. J. Appl. Fluid Mech. 2015;8(2):265-72. DOI |
10 | Kamel MS, Lezsovits F, Hussein AK. Experimental studies of flow boiling heat transfer by using nanofluids: A critical recent review. J. Therm. Anal. Calorim. 2019;138:4019-43. DOI |
11 | Hussein AK, Li D, Kolsi L, Kata S, Sahoo B. A review of nano fluid role to improve the performance of the heat pipe solar collectors. Energy Procedia. 2017;109:417-24. DOI |
12 | Rostami S, Sepehrirad M, Dezfulizadeh A, Hussein AK, Shahsavar GA, Shadloo MS. Exergy optimization of a solar collector in flat plate shape equipped with elliptical pipes filled with turbulent nanofluid flow: A study for thermal management. Water. 2020;12(8):2294. DOI |
13 | Ali B, Hussain S, Nie Y, Hussein AK, Habib D. Finite element investigation of Dufour and Soret impacts on MHD rotating flow of Oldroyd-B nanofluid over a stretching sheet with double diffusion Cattaneo Christov heat flux model. Powder Technol. 2021;377:439-52. DOI |
14 | D Li, Z Li, Y Zheng, C Liu, AK Hussein, X Liu. Thermal performance of a PCM-filled double-glazing unit with different thermophysical parameters of PCM. Sol. Energy. 2016;133:207-20. DOI |
15 | Hussein AK. Applications of nanotechnology in renewable energies-A comprehensive overview and understanding. Renew. Sustain. Energy Rev. 2015;42:460-76. DOI |
16 | Xiong Q, Hajjar A, Alshuraiaan B, Izadi M, Altnji S, Shehzad SA. State-of-the-art review of nanofluids in solar collectors: A review based on the type of the dispersed nanoparticles. J. Clean. Prod. 2021;310:127528. DOI |
17 | Hussein AK. Applications of nanotechnology to improve the performance of solar collectors – Recent advances and overview. Renew. Sustain. Energy Rev. 2016; 62: 767-92. DOI |
18 | Hussein AK, Walunj AA, Kolsi L. Applications of nanotechnology to enhance the performance of the direct absorption solar collectors. J. Therm. Eng. 2016;2(1):529-40. DOI |
19 | Mingo N, Stewart DA, Broido DA, Srivastava D. Phonon transmission through defects in carbon nanotubes from first principles. Phys. Rev. B. 2008;77(3):033418. DOI |
20 | Sevik C, Sevinçli H, Cuniberti G, Çağın T. Phonon engineering in carbon nanotubes by controlling defect concentration. Nano Lett. 2011;11(11):4971-7. DOI |
21 | Kim P, Shi L, Majumdar A, McEuen PL. Thermal transport measurements of individual multi-walled nanotubes. Phys. Rev. Lett. 2001;87(21):215502. DOI |
22 | Chang C, Okawa D, Garcia H, Majumdar A, Zettl A. Breakdown of Fourier’s Law in nanotube thermal conductors. Phys. Rev. Lett. 2008;101(7):075903. DOI |
23 | Sääskilahti K, Oksanen J, Volz S, Tulkki J. Frequency-dependent phonon mean free path in carbon nanotubes from nonequilibrium molecular dynamics. Phys. Rev. B. 2015;91(11):115426. DOI |
24 | Gspann TS, Juckes SM, Niven JF, Johnson MB, Elliott JA, White MA, Windle AH. High thermal conductivities of carbon nanotube films and micro-fibres and their dependence on morphology. Carbon. 2017;114:160-8. DOI |
25 | Zhang X, Zhou WX, Chen XK, Liu YY, Chen KQ. Significant decrease in thermal conductivity of multi-walled carbon nanotube induced by inter-wall van der Waals interactions. Phys. Lett. A 2016;380(21):1861-4. DOI |
26 | Goh B, Kim KJ, Park CL, Kim ES, Kim SH, Choi J. In-plane thermal conductivity of multi-walled carbon nanotube yarns under mechanical loading. Carbon. 2021;184:452-62. DOI |
27 | Koirala P, Werken NVD, Lu H, Baughman RH, Ovalle-Robles R, Tehrani M. Using ultra-thin interlaminar carbon nanotube sheets to enhance the mechanical and electrical properties of carbon fiber reinforced polymer composites. Compos. Part B. 2021;216:108842. DOI |
28 | Su C, Wang X, Ding L, Yu P. Enhancement of mechanical behavior of resin matrices and fiber reinforced polymer composites by incorporation of multi-wall carbon nanotubes. Polym. Test. 2021;96:107077. DOI |
29 | Han Z, Fina A. Thermal conductivity of carbon nanotubes and their polymer nanocomposites: A review. Prog. Polym. Sci. 2011;36(7):914-44. DOI |
30 | Hassanzadeh-Aghdam MK, Ansari R. Thermal conductivity of shape memory polymer nanocomposites containing carbon nanotubes: A micromechanical approach. Compos. Part B. 2019;162:167-77. DOI |
31 | Mayhew E, Prakash V. Thermal conductivity of high performance carbon nanotube yarn-like fibers. J. Appl. Phys. 2014;115(17):174306. DOI |
32 | Behabtu N, Young CC, Tsentalovich DE, Kleinerman O, Wang X, Ma AWK, Bengio EA, Waarbeek RFT, Jong JJD, Hoogerwerf RE, Fairchild SB, Ferguson JB, Maruyama B, Kono J, Talmon Y, Cohen Y, Otto MJ, Pasquali M. Strong, light, multifunctional fibers of carbon nanotubes with ultrahigh conductivity. Science. 2013;339(6116):182-6. DOI |
33 | Misak HE, Mall S. Electrical conductivity, strength and microstructure of carbon nanotube multi-yarns. Mater. Design. 2015;75:76-84. DOI |
34 | Wu AS, Chou TW. Carbon nanotube fibers for advanced composites. Mater. Today. 2012;15(7-8):302-10. DOI |
35 | Korab J, Štefánik P, Kavecký Š, Šebo P, Korb G. Thermal conductivity of unidirectional copper matrix carbon fibre composites. Compos. Part A Appl. Sci. 2002;33(4):577-81. DOI |
36 | Cohen Y, Ya’akobovitz A. The influence of thermal loads on the physical properties of carbon nanotubes forests. Microelectron. Eng. 2021;247:111575. DOI |
37 | Jagannatham M, Chandran P, Sankaran S, Haridoss P, Nayan N, Bakshi SR. Tensile properties of carbon nanotubes reinforced aluminum matrix composites: A review. Carbon. 2020;160:14-44. DOI |
38 | Azarniya A, Azarniya A, Sovizi S, Hosseini HRM, Varol T, Kawasaki A, Ramakrishna S. Physicomechanical properties of spark plasma sintered carbon nanotube-reinforced metal matrix nanocomposites. Prog. Mater. Sci. 2017;90:276-324. DOI |
39 | Misak HE, Mall S. Investigation into microstructure of carbon nanotube multi-yarn. Carbon. 2014;72:321-7. DOI |
40 | Koziol K, Vilatela J, Moisala A, Motta M, Cunniff P, Sennett M, Windle A. High-performance carbon nanotube fiber. Science. 2007;318(5858):1892. DOI |
41 | Zhan H, Chen YW, Shi QQ, Zhang Y, Mo RW, Wang JN. Highly aligned and densified carbon nanotube films with superior thermal conductivity and mechanical strength. Carbon. 2022;186:205-14. DOI |
42 | Li S, Zhang X, Zhao J, Meng F, Xu G, Yong Z, Jia J, Zhang Z, Li Q. Enhancement of carbon nanotube fibres using different solvents and polymers. Compos. Sci. Technol. 2012;72(12):1402-7. DOI |
43 | Zawilski BM, Littleton RT, Tritt TM. Description of the parallel thermal conductance technique for the measurement of the thermal conductivity of small diameter samples. Rev. Sci. Instrum. 2001;72(3):1770-4. DOI |
44 | Zawilski BM, Tritt TM. Dynamic measurement access, a new technique for fast thermal conductivity measurement. Rev. Sci. Instrum. 2001;72(10):3937-9. DOI |
45 | Jakubinek M, Niven JF, Johnson MB, Ashrafi B, Kim KS, Simard B, White MA. Thermal conductivity of bulk boron nitride nanotube sheets and their epoxy-impregnated composites. Phys. Status Solidi A. 2016;213(8):2237-42. DOI |
46 | Pöhls JH, Johnson MB, White MA, Malik R, Ruff B, Jayasinghe C, Schulz MJ, Shanov V. Physical properties of carbon nanotube sheets drawn from nanotube arrays. Carbon. 2012;50(11):4175-83. DOI |
47 | Niven JF, Johnson MB, Juckes SM, White MA, Alvarez NT, Shanov V. Influence of annealing on thermal and electrical properties of carbon nanotube yarns. Carbon. 2016;99:485-90. DOI |
48 | Jakubinek MB, Johnson MB, White MA, Jayasinghe C, Li G, Cho W, Schulz MJ, Shanov V. Thermal and electrical conductivity of array-spun multi-walled carbon nanotube yarns. Carbon. 2012;50(1):244-8. DOI |
49 | ISO 1973:2021. Textile fibres – Determination of linear density – Gravimetric method and vibroscope method. Edition: 3, Number of pages: 10, ICS Code: 59.060.01 Textile fibres in general *Including mixtures of fibres. Geneva, Switzerland: International Organization for Standardization. 2021. |
50 | ASTM D1577-07(2018). Standard test methods for linear density of textile fibers. Book of Standards Volume: 07.01, Developed by Subcommittee: 58, Number of pages: 11, ICS Code: 59.060.01 Textile fibres in general *Including mixtures of fibres. West Conshohocken, Pennsylvania, United States: ASTM International. 2018. DOI |
51 | Gonnet P, Liang Z, Choi ES, Kadambala RS, Zhang C, Brooks JS, Wang B, Kramer L. Thermal conductivity of magnetically aligned carbon nanotube buckypapers and nanocomposites. Curr. Appl. Phys. 2006;6(1):119-22. DOI |
52 | Hone J, Llaguno MC, Nemes NM, Johnson AT. Electrical and thermal transport properties of magnetically aligned single wall carbon nanotube films. Appl. Phys. Lett. 2000;77(5):666-8. DOI |
53 | Emmerich FG. Young’s modulus, thermal conductivity, electrical resistivity and coefficient of thermal expansion of mesophase pitch-based carbon fibers. Carbon. 2014;79:274-93. DOI |
54 | Jang D, Lee S. Correlating thermal conductivity of carbon fibers with mechanical and structural properties. J. Ind. Eng. Chem. 2020;89:115-8. DOI |
55 | Ericson LM, Fan H, Peng H, Davis VA, Zhou W, Sulpizio J, Wang Y, Booker R, Vavro J, Guthy C, Parra-Vasquez ANG, Kim MJ, Ramesh S, Saini RK, Kittrell C, Lavin G, Schmidt H, Adams WW, Billups WE, Pasquali M, Hwang WF, Hauge RH, Fischer JE, Smalley RE. Macroscopic, neat, single-walled carbon nanotube fibers. Science. 2004;305(5689):1447-50. DOI |
56 | Liu P, Fan Z, Mikhalchan A, Tran TQ, Jewell D, Duong HM, Marconnet AM. Continuous carbon nanotube-based fibers and films for applications requiring enhanced heat dissipation. ACS Appl. Mater. Interfaces. 2016;8(27):17461-71. DOI |
57 | Qiu J, Terrones J, Vilatela JJ, Vickers ME, Elliott JA, Windle AH. Liquid infiltration into carbon nanotube fibers: Effect on structure and electrical properties. ACS Nano. 2013;7(10):8412-22. DOI |
58 | Aliev AE, Guthy C, Zhang M, Fang S, Zakhidov AA, Fischer JE, Baughman RH. Thermal transport in MWCNT sheets and yarns. Carbon. 2007;45(15):2880-8. DOI |
Cite this article:
Chen, J. Effects of structure, purity, and alignment on the heat conduction properties of a nanostructured material comprising carbon nanotubes. DYSONA – Applied Science, 2022;3(2): 46-55. doi: 10.30493/das.2022.327865