Kaysse Ibrahim 1*; Michel Matar 2; Hayam A. Aly 3,4
1, Department of equipment and machinery engineering, Faculty of Technical Engineering, University of Tartous, Tartous, Syria
2, Mechanical Engineering Department, Beirut Arab University, Tripoli 1301, Lebanon
3, Department of Metallurgical and Materials Engineering, Faculty of Petroleum and Mining Engineering, Suez University, Suez 43512, Egypt
4, Central Metallurgical Research and Development Institute (CMRDI), Helwan 11421, Egypt
E-mail:
kay.ibra7@gmail.com
Received: 02/12/2024
Acceptance: 10/04/2025
Available Online: 12/04/2025
Published: 01/07/2025

Manuscript link
http://dx.doi.org/10.30493/DAS.2025.491672
Abstract
This study examined the impact of different combinations of chromium (5, 10, and 15%) and molybdenum (0.5, 2, 4, and 6%) content on steel samples fabricated using powder metallurgy. The powder amalgamation was compacted using a uniaxial press at a pressure of 686.7 MPa. The samples were sintered in a sealed furnace under argon gas, with a heating rate of 7°C/min, annealing temperature of 500 °C, and sintering temperature of 1150 °C for two hours, followed by cooling at 10 °C/min. The Rockwell surface hardness (HRC) was assessed for the sintered specimens. The dry sand/rubber wheel wear test (ASTM G65) was performed with a normal load of 130 N, a rubber wheel rotational speed of 200 rpm, and 1000 and 6000 revolutions, during which volume loss and wear coefficients were determined. Chromium and molybdenum concentrations directly influence the surface hardness and abrasive wear resistance of samples produced via powder metallurgy. Sintered samples exhibiting surface hardness of up to 80 HRC and exceptional abrasive wear resistance, with wear coefficients not surpassing 2.5×10-14 mm²/N, were produced. The findings indicated an enhancement in hardness and wear resistance with elevated levels of molybdenum and chromium.
Keywords: Steel, Chromium, Molybdenum, Wear resistance, Surface hardness, Sintering
Introduction
Molybdenum is an essential metal in steel applications that function at elevated temperatures [1-4]. Molybdenum coatings on special steel, particularly Ni-Cr-Mn steel, have garnered considerable interest for their wear-resistant and mechanical qualities [5][6].
The wear characteristics of (Fe–C–Ni–Mo) and (Fe–C–Mo) steel have been examined in both sintered and sintered/heat-treated specimens. Heat-treated steel demonstrates reduced wear rates owing to its superior toughness and resistance to plastic deformation, with molybdenum additions enhancing wear resistance through the development of bainitic microstructures [7]. Augmenting the molybdenum content in Fe–C–Mo steel alloys produced via powder sintering significantly improves sliding wear resistance, due to the development of a bainitic microstructure. Additionally, increasing the sintering temperature enhances the wear resistance of Fe–C–Mo steel [8].
Experiments indicate that discs made from untreated Fe–42at%Mo steel demonstrate greater wear resistance compared to ASTM 52100 steel, attributable to enhanced fracture resistance and elevated hardness [9]. The incorporation of molybdenum into plain carbon steel enhances wear resistance by facilitating the development of solid-phase carbides and molybdenum particles [10]. Elevating molybdenum content enhances true stress-strain values, leading to augmented yield strength, ultimate tensile strength, and toughness. Moreover, with the increase in Mo content, abrasion wear resistance and hardness also increase [11].
Powder metallurgy is an appealing technique due to its cost and material efficiency compared to conventional casting and forging methods, providing enhanced control over dimensions and weight. Powder mixtures of iron, carbon, and manganese are utilized in applications including heat-resistant bearings, brake discs, self-lubricating bearings, flanges, and other components resistant to wear and corrosion [12]. This process process is affected by various parameters, including mixing technique, constituent element ratios, sintering temperature, thermal gradient, sintering duration, sintering atmosphere, powder compaction method, and applied pressure for creating green samples.
Unlike conventional shaping methods such as casting, sintering is more of a chemical reaction than a metal-forming process, with each of the previously listed components directly influencing the final characteristics of sintered samples. Consequently, researchers have examined the dry wear characteristics of sintered and non-sintered specimens of low- and medium-carbon steel, discovering analogous wear behavior in both sample types [13]. However, the wear behavior of samples produced through powder sintering necessitates additional investigation, as the sintering process is particularly affected by the chemical composition of the powder blend.
Based on the previous debates, the significance of molybdenum in improving wear resistance, hardness, and toughness is evident. Nevertheless, the investigation of the synergistic impact of differing quantities of molybdenum and chromium in steel samples produced through powder sintering requires further research. This study seeks to investigate this effect and its influence on enhancing wear resistance under dry abrasion conditions caused by friction with solid particles. Additionally, the relationship between surface hardness and wear behavior of samples prepared by powder metallurgy will be determined.
Material and Methods
Materials
This study utilized various high-purity powders to prepare the samples under examination. The primary substance utilized was iron powder (Avonchem, 99.5% purity). Fine particle (50 μm) graphite powder, essential for lubricating and improving the mechanical characteristics of sintered materials, was obtained from Lobachemie.
The alloying constituents, namely chromium powder (Titanblotechtd, 99.0% purity), manganese powder (Chem-Lab NV, 99.9% purity), molybdenum powder (Riedel-de Haën, 99.7% purity) were used. Copper powder (AVONCHEM, 99.7% purity), nickel powder (AVONCHEM, 99.9% purity), and silicon powder (Riedel-de Haën, 97% purity) were employed to examine their influence on the mechanical properties of the sintered specimens. A lubricant, zinc stearate powder, was utilized to diminish friction during manufacturing and was procured from Avonchem.
The precise percentage proportions of these components in the tested specimens are presented in Table 1. This research primarily aimed to examine the influence of varied molybdenum contents (0.5%, 2%, 4%, and 6% by weight) in conjunction with varying chromium percentages (5%, 10%, and 15%) on the mechanical properties of the sintered samples.
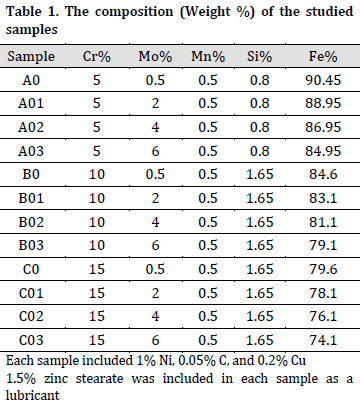
Methodology
The graphite powder was initially dried at 120°C for two hours to remove any residual moisture. Thereafter, the weights of each element were ascertained according to the designated percentage compositions of the alloying components for each sample (Table 1). The samples were precisely weighed using a high-precision balance (Precisa 205 A SCS) with a sensitivity of 0.0001 g. To improve the compressibility of the powders during pressing, 1.5% zinc stearate was included as a lubricant. Subsequent to the preparation of each batch in accordance with the designated percentage compositions of the materials, each sample was transferred into a V-shaped mixer (Fig. 1 A and B). The mixture was subsequently revolved on a shaft for 30 minutes at a velocity of 90 rpm.
The apparent density (g/cm³) of the powders was assessed, taking into account the die movement required for compressing and densifying the powder, along with the management of the compacts’ behavior during the sintering process. No notable variation was seen in the average apparent density of all mixes, recorded at 1.988 g/cm³.
Upon completion of the mixing process, the samples were shaped through uniaxial pressing in hardened steel molds with a hardness of 60 HRC, fabricated in accordance with the American standard ASTM B925-03. The powder was meticulously loaded into the molds to avert any displacement of the mold components. Subsequently, the samples were pressed using a hydraulic press with a capacity of 2000 kilonewtons (Perrier) located at the Syrian Construction and Building Company Laboratory – Tartous Branch. A pressure of 686.7 MPa, equivalent to 105T, was exerted on the wear samples at a compaction rate of 0.127 mm/sec. This pressure was sustained for 30 seconds to mitigate elastic rebound. Thereafter, the pressure was released, and the green sample (post-compaction) was cautiously extracted. The mold was then thoroughly cleaned to eliminate any residue and refilled with the subsequent batch of powder. This procedure culminated in the formation of the green samples (Fig. 1 C-E). The green samples (Fig. 1 F) demonstrate comparatively inferior mechanical qualities, necessitating meticulous handling and storage until the sintering process is executed. The green density was determined with a high-precision balance, yielding a value of 4.3 g/cm³.
The sintering procedure was conducted by positioning the samples in a sealed Linn HT 1600 M furnace inside an argon environment (Fig. 1 G-I). The procedure entailed positioning the samples in the furnace beforehand, providing sufficient separation between each sample. The furnace was thereafter heated at a rate of 7°C per minute to a temperature of 500°C and maintained at this temperature for one hour. This procedure facilitated grain annealing and the elimination of leftover nitrogen and oxygen to avert gas bubble formation or distortions in the samples’ morphology. The temperature was subsequently increased to the final sintering temperature of 1150°C and maintained for two hours. Cooling was thereafter performed in the furnace at a rate of 10°C per minute (Fig. 1 J).
Testing
Hardness testing
The hardness testing of the examined samples was performed in line with ASTM E18-15 for Rockwell C hardness (HRC) values. The tests were conducted on rectangular samples measuring 6 x 2.5 x 0.8 cm (Fig. 1 K), utilizing a universal hardness tester (model HBRV-187.5) at the Higher Institute of Applied Sciences and Technology. A diamond spheroconical indenter with a tip radius of 0.2 mm was employed. A preliminary load of 10 kgf was applied and maintained for 4 seconds, then increasing to a maximum load of 150 kgf at a rate of 2.5 mm/s. The maximum load was sustained for 20 seconds to reduce elastic recovery. Five measurements were obtained, and their arithmetic mean was computed.
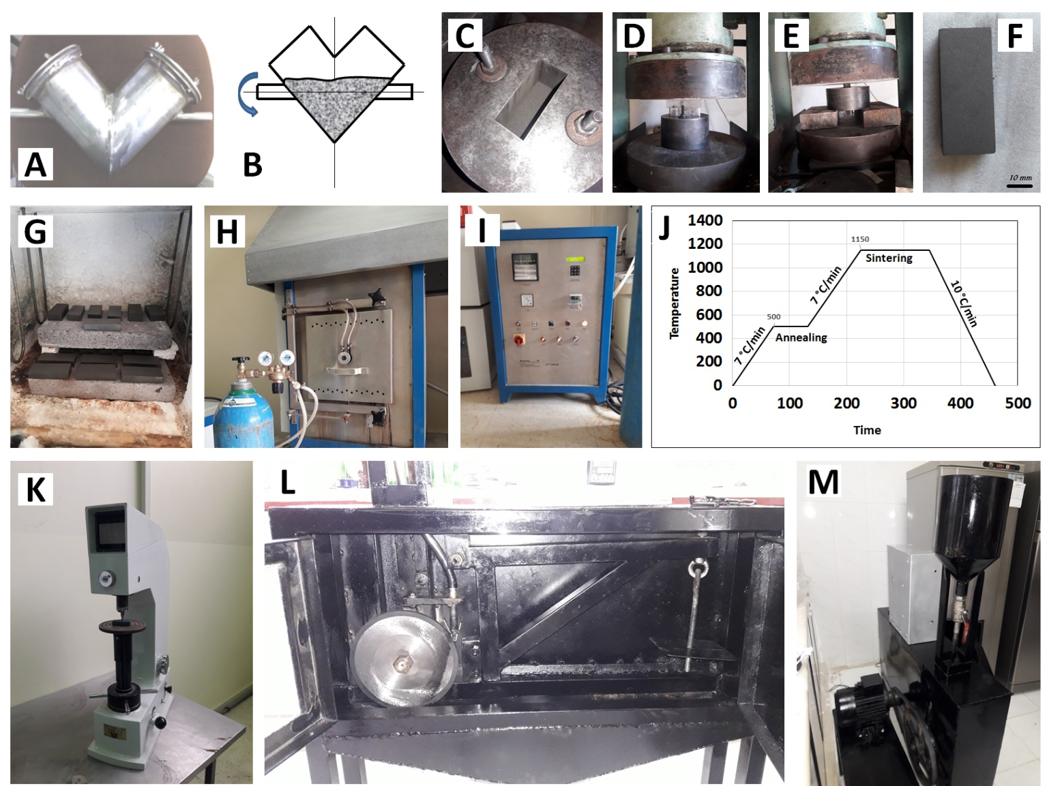
Wear test
The wear testing utilized a dry sand/rubber wheel abrasion tester, specifically designed and produced for this study in accordance with ASTM G65-04 requirements. The abrasive material employed was AFS 50/70 grade silica sand, pre-dried in a thermal oven at 105°C until it reached a consistent weight to remove moisture. The device comprises a steel wheel encased in molded chlorobutyl rubber and includes a cycle counter sensor that signals a PLC unit to halt the engine by braking. Tests were conducted at a velocity of 200 rpm on samples of 6 x 2.5 x 0.8 cm, with a sand flow rate of 300-400 g/min. The samples’ surface roughness was regulated to a maximum of Ra = 2 μm (Fig. 1 L and M).
Two testing protocols were implemented: Procedure A, which entailed applying a force of 130 N with a rubber wheel rotation of 6000 rpm, resulting in an abrasion distance of 4309 m; and Procedure E, which utilized the same weight at a rotation speed of 1000 rpm, equating to a distance of 718 m. Weight loss was assessed by measuring the mass of the samples before and after testing with a precision balance (Precisa 205 A SCS) with an accuracy of 0.0001 g. The reduction in weight was subsequently transformed into volumetric loss utilizing the following equation:

As the rubber wheel wears and its diameter decreases, the scratching abrasion generated during the test is proportionally reduced, leading to a potential underestimation of the actual material loss. Consequently, the direct measurement of volume loss under these conditions may not accurately reflect the true abrasion rate. To compensate for this variation, the adjusted volume loss (AVL) is calculated, which normalizes the abrasion data to correspond to the original standard wheel diameter of 228.6 mm. In accordance with ASTM G65-04, the adjusted volume loss can be determined using the following formula:

The tests were conducted at laboratory temperature with three replicates for each test sample, and the arithmetic mean of these replicates was recorded as the final value. The wear coefficient K (m2/N) was calculated based on the relationship between the wear volume V (m3), the distance traveled L (m), and the applied normal load on the sample Np (N), using the following equation [14]:

Wear surface scanning
The wear surfaces of the specimens were examined using an optical microscope. To obtain high-resolution three-dimensional surface topography and surface roughness data, a Keyence VK-X100 3D laser scanning confocal microscope was employed. Prior to scanning, all specimens were carefully cleaned to remove dust, oil, and debris, followed by rinsing with ethanol to ensure surface clarity. A scanning area of 50 × 32 mm was selected, centered precisely within the abraded region of each specimen. The arithmetic average surface roughness (Ra) was measured along the central line of the scanned area.
Results and Discussion
The results of hardness test show that incorporating molybdenum is distinctly observable and is directly correlated with the chromium percentage of the alloy (Fig. 2 A). With a chromium content of 5%, an increase in molybdenum content from 0.5% to 6% results in a rise in surface hardness from 41.16 HRC to 52.83 HRC, respectively. At chromium concentrations of 10% and 15%, the pattern was analogous, with surface hardness values rising from 62.62 HRC to 75.66 HRC and from 54.12 HRC to 80.41 HRC, respectively. The results indicate a synergistic link between chromium and molybdenum levels in iron-based samples produced via powder metallurgy, implying that the sintering process functions more as a chemical reaction than a conventional forming process. No notable variations in hardness values were detected between the chromium concentrations of 15% and 10% at identical molybdenum content in both groups, necessitating additional exploration in subsequent research. The observed enhancement of steel hardness at a chromium concentration of 5% due to elevated molybdenum levels is ascribed to the proliferation of molybdenum carbide particles inside the austenitic matrix, at the detriment of iron carbides [11].
The influence of molybdenum and chromium concentrations on wear volume during Procedure A (abrasion distance of 4309 m) was visualized (Fig. 2 B). The wear volume markedly diminished with elevated molybdenum concentration at 5% chromium, decreasing from 189.26 mm³ to 28.69 mm³, attributable to the presence of hard carbide phases and molybdenum particles [10]. With an increase in chromium concentration to 10% and 15%, the wear volume diminishes from 118.65 mm³ to 17.62 mm³ and from 214.23 mm³ to 18.65 mm³, respectively. It is worth noting that any combination of Mo>5% and Cr>9% resulted in a wear volume less than 25 mm3 under Procedure A. Similarly, any combination of Cr>13% with Mo content of 4% or more resulted in similar decreased wear volumes. As for Procedure E, a similar pattern was observed, as wear volume decreased with the increase of Mo and Cr content (Fig. 2 C). Any combination of Cr>8% and Mo>3% resulted in a wear volume less than 10 mm³ and any combination of Cr>9% and Mo>5% resulted in a wear volume less than 5 mm³. These observations are mainly attributed to the presence of chromium and molybdenum carbides [15]. The preceding values are regarded as favorable for dry wear resistance, attributable to the bainitic structure that develops in the presence of molybdenum in the powder metallurgy samples [16].
No substantial alterations in wear coefficient values were noted between the two processes at each molybdenum level with 5% chromium (Fig. 2 D and E). The wear coefficients diminished as molybdenum content increased, attributed to the enhancement in hardness values [17]. The minimum wear coefficient values were observed for samples A02 and A03 (2.5×10⁻¹³ mm²/N) following an abrasion distance of 4309 m. The wear coefficients markedly diminished with an increase in chromium content to 10%, attaining the minimum values at 6% molybdenum (3.14×10-14 mm²/N) following Procedure A (an abrasion distance of 4309 m). In order to achieve wear coefficients less than 10⁻¹³ under both procedures, a Cr>8% and Mo>3% were required. The similar wear behavior regardless of abrasion distance suggests that the tribological alterations were inadequate to modify the wear behavior. This indicates a more robust structure, attributed to the substantial rise in carbide content at the grain boundaries, which enhances wear resistance [18].
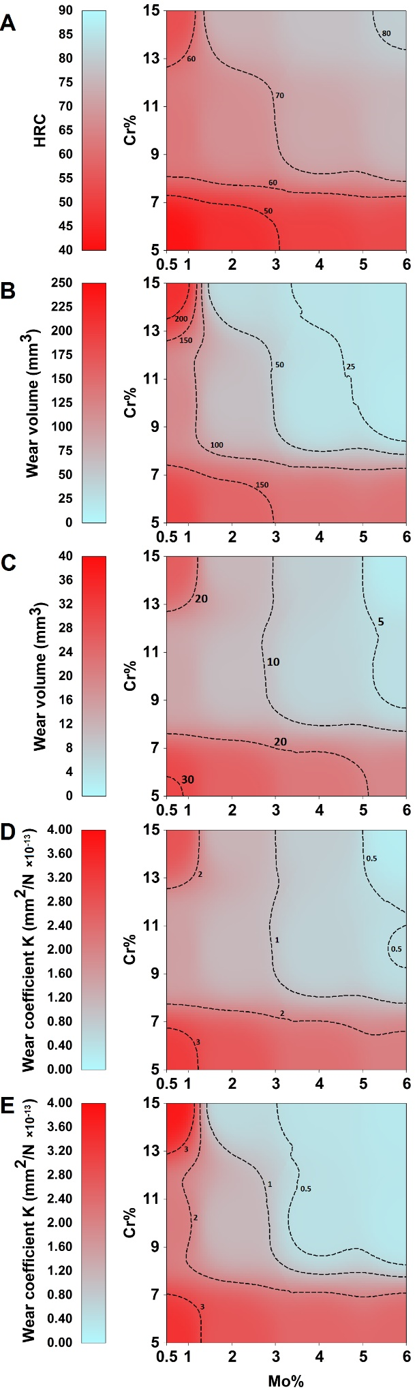
Wear surface morphology scans of the tested samples were prepared after Procedures E and A (Figs. 3 and 4). The figures showed an irregular deformation at low molybdenum levels and 5% chromium (A0, B0, C0) following Procedure A (an abrasion distance of 4309) (Fig. 3). This observation aligns with the understanding that lower concentrations of alloying elements result in less stable microstructures [19]. Nonetheless, this deformation becomes increasingly prevalent with higher concentrations of chromium and molybdenum, presenting as micro-scale abrasions (scratches). The deformation becomes increasingly erratic, and the surface roughness markedly escalates, attaining values between 21.321 μm and 25.337 μm as a result of the elevated concentrations of molybdenum and chromium carbides. Surface roughness was minimal at 10% chromium (B0, B01, B02, B03), varying from 8.662 μm to 18.623 μm, and escalated with increased molybdenum concentration.
The increased presence of red coloration in 3D scans of Procedure E suggests a comparatively rougher or less worn surfaces, while the more uniform or lower-elevation colors observed in Procedure A indicate more significant surface abrasion. In Procedure E (Fig. 4), the deformation intensity was reduced, and the surface roughness values were significantly lower than those of Procedure A, particularly at elevated chromium and molybdenum concentrations. This is due to the friction surface being less susceptible to distortion at the outset of wear. Nonetheless, as the sliding distance increased throughout the dry sand abrasion test utilizing the rubber wheel, tribological alterations commenced on the friction surfaces. Carbides began to generate abrasive particles, exacerbating the wear of the friction surface, which possessed a lower hardness relative to the carbide-rich regions.
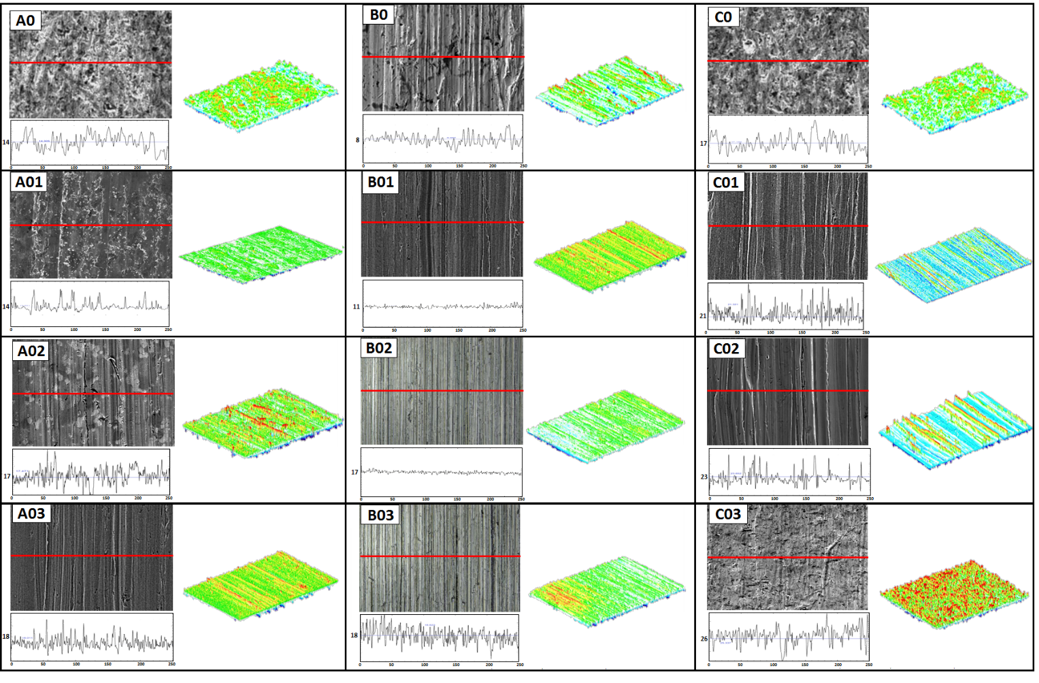
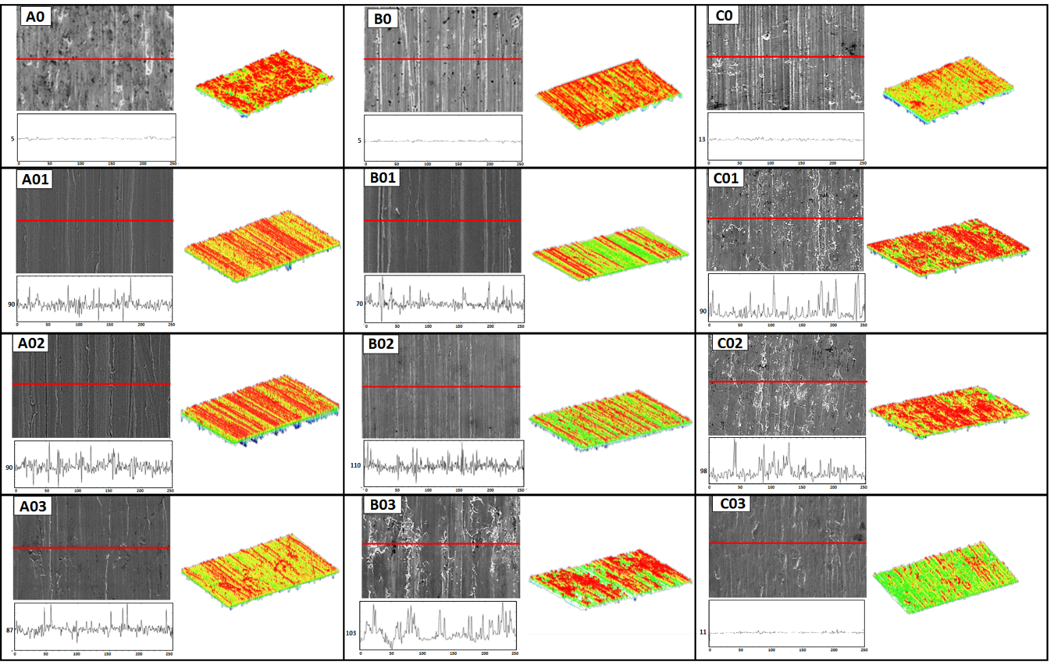
Conclusions
The research indicates that elevated levels of chromium and molybdenum markedly enhance the hardness, wear resistance, and surface durability of iron-based powder metallurgy specimens. Increased molybdenum concentration, especially in an austenitic matrix, facilitates the production of molybdenum carbide particles, hence improving surface hardness and wear resistance by diminishing wear volume. The synergistic connection between chromium and molybdenum enhances mechanical characteristics.
Elevating chromium and molybdenum concentrations significantly diminished wear coefficients and enhanced surface hardness. Nevertheless, wear behavior does not exhibit consistent changes across prolonged sliding distances, suggesting that elements beyond surface hardness, including thermally induced tribological alterations and microstructural characteristics, significantly influence wear resistance. The increased chromium content (10% and 15%) did not result in notable hardness enhancements, indicating a maximum limit for hardness improvement by chromium in this material matrix.
Consequently, the subsequent conclusions may be inferred:
- The ratios of chromium and molybdenum greatly influence the surface hardness and wear resistance of samples produced through powder metallurgy.
- Sintered samples can attain a surface hardness of up to 80 HRC and exhibit remarkable wear resistance, with wear coefficient values as low as 2.5×10-14 mm²/N, which are advantageous for durability against wear.
- Initial wear induces micro-cutting deformation, subsequently leading to the emergence of micro-cracking phenomena as wear advances.
- Surface roughness escalates with elevated molybdenum concentration and increases with the sliding distance, attributable to the influence of molybdenum carbides.
- Future research should investigate the reason behind increments in chromium levels over 10% not resulting in substantial alterations in hardness, possibly suggesting a saturation threshold for chromium’s influence on hardness in these materials.
- Considering that wear resistance is contingent upon both hardness and tribological modifications, it would be advantageous to investigate the microstructural evolution under conditions of elevated friction and temperature.
- Investigating other alloying elements or carbide formers, such as vanadium or tungsten, may yield more insights and perhaps enhance wear resistance while maintaining a balance between hardness and ductility.
- Evaluating alternate wear methodologies for diverse application-specific situations (e.g., humid environments or varying abrasives) may provide insights into the extensive applicability of these alloy compositions across several industries.
References
- Cho K, Kawahara N, Yasuda HY. Effect of Grain Refinement on Room Temperature Ductility of Ferritic Heat-resistant Alloys Strengthened by NiAl Precipitates. ISIJ Int. 2020;60(10):2285-90. DOI
- Cho K, Ikeda K, Yasuda HY. Improvement of room and high temperature tensile properties of NiAl-strengthened ferritic heat-resistant steels through Mo addition. Mater. Sci. Eng. A. 2018;728:239-50. DOI
- Calderon H, Fine ME. Coarsening kinetics of coherent NiAl-type precipitates in Fe-Ni-Al and Fe-Ni-Al-Mo alloys. Mater. Sci. Eng. 1984;63(2):197-208. DOI
- Shi F, Qi Y, Liu C. Effects of Mo on the Precipitation Behaviors in High-Nitrogen Austenitic Stainless Steels. J. Mater. Sci. Technol. 2011;27(12):1125-30. DOI
- Laribi M, Vannes AB, Treheux D. On a determination of wear resistance and adhesion of molybdenum, Cr-Ni and Cr-Mn steel coatings thermally sprayed on a 35CrMo4 steel. Surf. Coat. Technol. 2006;200(8):2704-10. DOI
- Laribi M, Vannes AB, Treheux D. Study of mechanical behavior of molybdenum coating using sliding wear and impact tests. Wear. 2007;262(11-12):1330-6. DOI
- Straffelini G, Molinari A. Dry sliding behaviour of steam treated sintered iron alloys. Wear. 1992;159(1):127-34. DOI
- Ceschini L, Palombarini G, Sambogna G, Firrao D, Scavino G, Ubertalli G. Friction and wear behaviour of sintered steels submitted to sliding and abrasion tests. Tribol. Int. 2006;39(8):748-55. DOI
- Murakami T, Kaneda K, Nakano M, Mano H, Korenaga A, Sasaki S. Friction and wear properties of Fe-Mo intermetallic compounds under oil lubrication. Intermetallics. 2007;15(12):1573-81. DOI
- Kandavel TK, Chandramouli R, Manoj M, Manoj B, Gupta DK. Influence of copper and molybdenum on dry sliding wear behaviour of sintered plain carbon steel. Mater. Des. 2013;50:728-36. DOI
- Nasajpour A, Kokabi A, Davami P, Nikzad S. Effect of molybdenum on mechanical and abrasive wear properties of coating of as weld hadfield steel with flux-cored gas tungsten arc welding. J. Alloys Compd. 2016;659:262-9. DOI
- Mohan Raj AP, Selvakumar N, Narayanasamy R, Kailasanathan C. Experimental investigation on workability and strain hardening behaviour of Fe-C-Mn sintered composites with different percentage of carbon and manganese content. Mater. Des. 2013;49:791-801. DOI
- Lim SC, Isaacs DC, McClean RH, Brunton JH. The unlubricated wear of sintered steels. Tribol. Int. 1987;20(3):144-9. DOI
- Archard JF. Contact and Rubbing of Flat Surfaces. J. Appl. Phys. 1953;24(8):981-8. DOI
- Huang P, Liu R, Wu XJ, Yao MX. Mechanical properties and corrosion resistance of a novel Ni-Cr-Mo alloy. Adv. Eng. Mater. 2007;9(1-2):60-4. DOI
- Wang J, Danninger H. Dry sliding wear behavior of molybdenum alloyed sintered steels. Wear. 1998;222(1):49-56. DOI
- Xia T, Ma Y, Zhang Y, Li J, Xu H. Effect of Mo and Cr on the microstructure and properties of low-alloy wear-resistant steels. Materials. 2024;17(10):2408. DOI
- Li C, Teng J, Yang B, Ye X, Li Y. Effect of Carbon Content on Wear Behavior of Ni-Co-Cr-Mo-Cu Alloy. J. Mater. Eng. Perform. 2024;33(10):5085-99. DOI
- Herbirowo S, Syahrum M, Hasbi MY, Chandra SA, Ridlo FM, Adjiantoro B. Mechanical and microstructure properties of the Ni-Cr-Mo modified steel by heat treatment process. In IOP Conference Series: Materials Science and Engineering. IOP Publishing. 2019;541(1):012014. DOI
Cite this article:
Ibrahim, K., Matar, M., Aly, H. A. Influence of chromium and molybdenum content on wear resistance in steel samples fabricated via powder metallurgy. DYSONA – Applied Science, 2025; 6(2): 351-360. doi: 10.30493/das.2025.491672