Fawzia J. Shalsh 1*; Nagham Abdul Alrazzaq 1; Dhoha K. Nagimm 1; Muhammad Abdul Alrheem 1; Saffa Abedul Alrheem 1; Kolad Abd alalah 1
1, Industrial Microbiology Department, Directorate of Agricultural Research, Ministry of Science and Technology, Iraq
E-mail:
fawzia.jassim2015@gmail.com
Received: 18/09/2020
Acceptance: 23/02/2021
Available Online: 24/02/2021
Published: 01/04/2021

Manuscript link
http://dx.doi.org/10.30493/das.2020.220730
Abstract
Agricultural waste is a major environmental challenge, especially in developing countries. Lignocellulose biomass is a low-cost bioresource with great potential for bioethanol and bioproducts production. However, the high costs of the enzymic treatment restrict agricultural mass utilization. MixAlco process applied methane-inhibited route to convert environmental waste into carboxylate salts under non-sterile anaerobic fermentation conditions. In this study, the lime-treated agricultural residue of white sorghum biomass (80%) supplemented by chicken manure (20%) was fermented under anaerobic conditions in a stirred-tank bioreactor. The fermentation process resulted in an acid concentration of 21.03 g/L at a conversion rate of 54.4 % for the initial volatile solids. The fermentation products constituted mainly of acetic acid, followed by propanoic acid and ethanol. The current research indicates that the MixAlco biotechnology that uses mixed agricultural wastes as a fermentation material provides an economical substitute to chemicals and physical processing methods.
Keywords: Fermentation, Carboxylate platform, Carboxylic acids, Bioethanol, Volatile matter
Introduction
Bioethanol is a raw material for various food and pharmaceutical industries and has gained significant interest as a biofuel due to its economic and environmental advantages compared to fossil fuels. Biofuels reduce environmental pollution by reducing greenhouse gasses emission [1]. Its use is also an economical substitute for oil, especially in non-producing countries or those facing difficulties in extracting fossil fuels. The production of biofuels depends on the fermentation of sugars in various types of biomasses to produce bioethanol, biodiesel, and biogas. Many raw bio-materials contain lignocellulose biomass, such as wood, agricultural wastes, municipal solid wastes, and marine algae [2]. Bioethanol production process includes pretreatment stages, hydrolysis, fermentation, and product separation. The traditional converting of agricultural residues is usually done through simultaneous saccharification and fermentation (SSF) systems using costly specialized enzymes, which represents the most critical limitations in utilizing agricultural waste in bio-conversion [3][4].
Carboxylate platform (MixAlco) uses microbial cultures to convert lignocellulose biomass in agricultural residues to carboxylic acids under anaerobic fermentation conditions [5]. The main advantages of this process are that no need for sterile conditions or specific enzymes for fermentation, in addition to its capability of processing various sources of lignocellulose biomass for biofuel and bioproducts production [6][7]. Carboxylate platform development went through gradual stages from laboratory investigation (1991), pilot-scale (90.7 kg/day) (1998), demonstration plants (5 ton/day) (2007), and high capacity demonstration plant (100 ton/day) (2009) [6][8]. Furthermore, this technique was proven to be economically viable at both large and small scales to recycle various waste products [9][10]. It can convert concentrated carboxyl salts into a variety of useful chemicals and fuels [11].
Various carbohydrates and nutrients like protein, vitamins, and minerals are required to ferment raw material in MixAlco efficiently. Agricultural residues are rich in carbohydrates but low in the crucial nutrients for microbial growth. On the other hand, animal manure contains huge sums of supplements [12]. Therefore, the use of agricultural residues and animal manure combinations is considered an economically viable and environmentally friendly solution for the production of carboxylic acids, ketones, and mixed alcohols via carboxylate platforms [13]. The recommended ratio is 80%: 20% of the agricultural waste and animal manure, respectively [8][13]. The fermentation is a crucial aspect of the MixAlco process, which depends on the microbial community to convert environmental waste biomass to carboxylate compounds. Then, biofuel can be prepared whenever the chemical conversion of intermediate compounds occurs [14].
White sorghum has been the preferred crop biomass for fermentation to obtain methanol and ethanol [15-17]. Additionally, sorghum is among the highly adaptable cereal grasses [18][19]. The adaptation of the sorghum plant to semi-humid and semi-arid climates has expanded the geographical area for its production and its superiority over other types of grains. Sorghum requires no specific soil qualities or high fertilizer input. Additionally, sorghum demands minimal water requirement per dry tone of the crop, which is half the water requirement of sugar beet and one-third that of sugarcane or corn [20]. All the aforementioned reasons, in addition to the high yield (70-80 tons/ha of fresh matter) rendered sorghum as an economically viable crop for the production of biofuel [21].
Various organic material sources were used in MixAlco process [22], such as brown algae [10][23], sugarcane bagasse [24], corn stover [25][26], and many other agricultural byproducts. This study aimed to investigate the validity of using MixAlco process to produce different useful chemical compounds from biotreated sorghum biomass following the anti-methane pathway.
Materials and methods
Agricultural materials
White sorghum biomass (stalks, leaves, and grains) was obtained from a local market, placed separately in plastic bags, and stored in the freezer at -18 °C and relative humidity of 70% until used. White sorghum biomass was dried in an oven at 60 °C for 24h to remove moisture content. Then, the dry parts were milled separately using a blender and sieved through a 20 mesh screen (0.9 mm) [27][28]. The resulting white sorghum powder was treated with lime at a rate of 0.1 g Ca(OH)2 and 10 mL of water per gram of white sorghum. The chicken manure was obtained from the local market and dried at 105 °C in an oven, and placed in a tightly sealed container for further use.
Inoculum preparation for fermentation
Fermentation was initiated in batch approach with a concentration of 100g solids/l000 ml distilled water. Solids mixture was prepared with 90% lime-treated white sorghum biomass (1:1:0.5) of stalk: leaves: seeds (90g) and 10% analytical grade yeast extract powder (10g). Solids were added to a liter of water and inoculated with a pure culture of Trichoderma harzianum. This fermentation inoculum was incubated at 30±2 ºC for 7 days under non-sterile batch fermentation conditions to augment the natural microbial community coexisting with plant material [24].
The fermentation medium
The fermentation was conducted in a 1-L LAMBDA MINIFOR stirred tank bioreactor fermenter (Fig. 1). The fermentation medium consisted of lime-treated white sorghum biomass (at the same ratios above) and chicken manure at a ratio 80:20 g:g of sorghum to chicken manure in 500mL of water. Additionally, a nutrient mixture (50 ml) was added during the anaerobic fermentation as a supplementary nutrient source for the microorganisms. Nutrient mixture was prepared following [29], the mixture contained; KH2PO4 (16.3g), (NH4)2SO4 (16.3g), NaC1 (32.6g), MgSO47H2O (6.8g), CaC12H2O (4.4g), p-aminobenzoic acid (0.71g), Ca-pantothenate (0.71g), folic acid (0.35g), nicotinamide (0.71g), pyridoxal (0.35g), riboflavin (0.35g), thiamine (0.34g), biotin (0.14g), EDTA (0.35g), FeSO47H2O (0.14g), MnC12 (0.14g), CoC12 (0.014g), ZnSO47H2O (0.007g), NaMoO4 (0.0021g) and CuC12 (0.0007g) per liter. Furthermore, Sodium sulfide (0.275 g/L) and cysteine hydrochloride (0.275 g/L) were added under continuous nitrogen purge to support the anaerobic conditions of the fermentation medium. In order to repress methane formation, 120µl of iodoform solution (20 g CHL3 in 1000 ml ethanol) was added every 48 h throughout the fermentation [24]. Since the maximum pressure limit of the fermenter is 2atm, a daily gas venting was performed to prevent fermenter explosions. The experiment was conducted at a temperature of 48 ºC for 12days. To monitor the fermentation process, the fermenter was vented using a syringe attached to an air-tight tube connected to a water column filled with 70% ethanol. If the pH dropped to less than 7.0, ammonium bicarbonate was used to re-neutralize the medium. After fermentation, 3 ml sample of the fermented sorghum biomass was collected for later analysis.
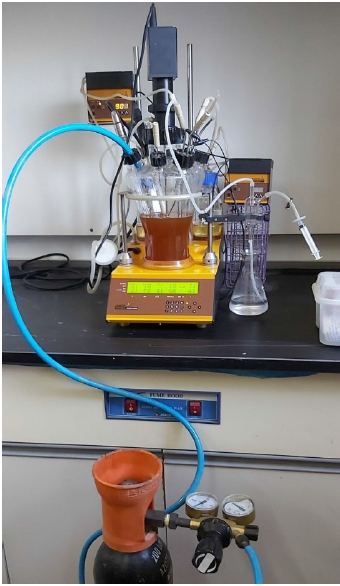
Analytical methods
Moisture content for sorghum biomass and the final fermentation solid residue was determined by placing 5 g of the milled white sorghum biomass (1:1:0.5 stalk: leaves: seeds) in the oven at 105 °C for 2 h until an observed constant weight. Moisture percentage was then calculated from the difference between the initial weight and the dry weight [30][31]. Dry Matter percentage was calculated as 100 – moisture content percentage.
Ash content for the white sorghum biomass mixture and final fermentation solid residue was calculated after 4 hours in the furnace at 550 °C as described by [18].

The volatile matter of white sorghum biomass mixture and final fermentation solid residue was calculated as described by [24][26].

Percentage of volatile matter (PVM) was calculated using the equation [30]:

The percentage of fixed carbon (PFC) was computed by subtracting the sum of PVMand PAC (percentage ash content) from 100, as shown in equation (4) [32].
PFC = 100% – (PAC+PVM) (4)

The content of total carbohydrates in white sorghum biomass was analyzed using the methods described by [30][33].
2.5. Gas chromatography-mass spectrometry (GC-MS) analysis
GC-MS was used to determine carboxylic compounds in sorghum biomass mixture hydrolysate [26][25]. For this purpose, A GC-MS instrument (GC-17A Ver.3 Shimadzu, Japan) equipped with an SGE BP21 25 m x 0.33 mm x 0.25μm column was used. Sampling time was 1 min injection with an initial temperature of 200 °C and an interface temperature of 250 °C. Control mode was splitless, and column inlet pressure was 15.0 kPa with a flow of 2.2 mL/min. Linear velocity was 58.4 cm/sec, and the split ratio was 10. A library search was carried out to identify the chromatographic peaks with consideration to the standards (0.50 mg/mL) that were run at the beginning and the end of the sample set.
Results and Discussion
White sorghum sample analysis
The analysis of white sorghum powder showed that it had a low moisture content (7.92%), and a low ash content (2.8%) which indicates that it can burn off easily in bioconversion prosses (Table 1). The low moisture content is critical in preserving sorghum during storage due to its association with biological factors that cause post-harvest damage and negatively influence nutritional and economic values. The current results are in accordance with other studies such as [34], who reported a moisture content range between 7.28% and 11.57% and lower than other studies such as [35] who reported a moisture range of 11 to 21 %. Furthermore, white sorghum ash content was reported to range from1.3% to 3.3% [36][37], which puts the current results within the normal range.

The analysis showed that 75.27% of the total powder weight was constituted of volatile matter. It was previously reported that the main volatile compounds in biomass were alcohols, alkanes, aldehydes, esters, aldehydes, carboxylic acids, ketones, pyrazines, and phenylenediamine [32], which individually affected by the used processing techniques [23]. The current result was higher than that of [14], who reported 63% total volatile matter. Similar to low moisture content, the high PVM value signifies an easy ignition of the biomass.
The total dry matter of white sorghum (92.37%) is within the range reported by [36] (96.20% to 97.5%). Fixed carbon is the amount of combustible solids content in fuel after the removal of volatile matter. The current result (21.06%) is comparable to the (19.06%) for wheat straw obtained by [31]. Carbohydrate content was 68% which is lower than that reported in sorghum biomass used in [38]. The primary carbohydrate compounds of sorghum is lignocellulose which, because of its high carbon content, can produce energy via heat or chemical processes.
Fermentation experiment
MixAlco route has utilized the growth of natural microbial community coexisting with sorghum biomass. The treated white sorghum biomass and chicken manure are easily digested via microorganisms [37]. During MixAlco process, fractions of the biodegradable biomass waste are utilized to produce enzymes that hydrolyze the cellulose into monomers such as glucose which is converted to volatile acids and alcohols due to the fermentation process. However, the involved enzymes action might be inhibited by the hydrolysis endproducts, through thermal denaturation, or due to absorption by natural sorghum components such as lignin [39]. Therefore, it is imperative to maintain certain fermentation conditions and use a proper material combination.
The result of the used batch fermentation parameters was calculated (Table 2). GC-MS analysis showed that the total acid concentration was 21.0 g/l with a conversion rate of 54.4% and a yield of 34%. The acid yield is the ratio of volatile solids in the substrate fed to the fermentor and converted to mixed acids due to the fermentation procedure. On the other hand, conversion rate refers to the digested volatile solids throughout fermentation from the total input volatile solids, which means that in the current study, more than half of sorghum biomass was converted to products such as volatile acids. Acetic acid constituted 54% of the total produced acids, followed by propionic acid with 26% and ethanol with 20%. Carboxylic acids production is a survival strategy attributed to the fact that when sources of energy and nutrients are available in abundance, the microbial community tend to produce compounds that can be utilized in periods of starvation [40]. Other compounds were detected via GC-MS analysis; however, they were present in insignificant concentrations such as G,5-Furandione, dihydro-3-methylene-, 2-Furancarboxaldehyde, 5-methyl-, Hydrogen chloride, Furfural, Cyclopentasiloxane, and decamethyl.

Previously, batch culture fermentation of treated bagasse (80%) and chicken manure (20%) resulted in a total carboxylic acid concentration of 56.1 g/L, which is the highest ever recorded using MixAlco method in a rotary fermenter with a conversion rate of 44% [24]. The second highest report was 40.8 g/L of total acid concentration with lime-treated rice straw (80%) and chicken manure (20%) [13]. On the other hand, a fermentation medium of swine manure (60%) and lime-treated corn stover (40%) resulted in the highest recorded conversion ratio (73%) with an acid concentration of 25.1 g/L [25].
Conclusion
In the current study, the biological transformation of white sorghum biomass was performed under operating conditions similar to the MixAlco process. The fermentation process resulted in a total carboxylic acid concentration of 21.03 g /L with a conversion of 54.4% of the digested biomass. The fermentation products were mainly constituted of acetic acid (54%), propionic acid (26%), and ethanol (20%). Therefore, replicating the current reported conditions at a commercial level is highly recommended to use the agricultural wastes of both sorghum cultivation and chicken industry and to support the energy sector.
References
1 | Bakhshayeshan-Agdam H, Salehi-Lisar SY, Zarrini G. Lignocellulosic Biofuel Production Technologies and Their Applications for Bioenergy Systems. In Biofuels Production–Sustainability and Advances in Microbial Bioresources. Springer, Cham. 2020:287-306. DOI |
2 | Dickson R, Fasahati P, Liu J. Optimal design for integrated macroalgae-based biorefinery via mixed alcohol synthesis. Elsevier. In Computer Aided Chemical Engineering 2019;46:253-8. DOI |
3 | Yano S. Enzymatic saccharification and fermentation technology for ethanol production from woody biomass. J. Japan Pet. Inst. 2015;58(3):128-34. DOI |
4 | Sóti V, Lenaerts S, Cornet I. Of enzyme use in cost-effective high solid simultaneous saccharification and fermentation processes. J. Biotechnol. 2018;270:70-6. DOI |
5 | Taco-Vasquez S, Holtzapple MT. Biomass conversion to hydrocarbon fuels using the MixAlcoTM process. Oil Gas Sci. Technol. 2013;68(5):861-73. DOI |
6 | Vasquez ST, Dunkleman J, Chaudhuri SK, Bond A, Holtzapple MT. Biomass conversion to hydrocarbon fuels using the MixAlco™ process at a pilot-plant scale. Biomass Bioenergy. 2014;62:138-48. DOI |
7 | Van Walsum GP, Flatt M, Doyle E, Adapala R. Application of the MixAlco Process to In-Situ Conversion of Dairy Manure and Chipped Yard Waste For Production of Fuels and Chemicals. In The 2005 Annual Meeting. 2005. |
8 | Granda CB, Holtzapple MT, Luce G, Searcy K, Mamrosh DL. Carboxylate platform: the MixAlco process part 2: process economics. Appl. Biochem. Biotechnol. 2009;156(1):107-24. DOI |
9 | Engelberth AS, Clayton Wheeler M, Peter van Walsum G. Techno‐economic comparison of three scenarios for upgrading a hemicellulose‐rich pre‐pulping extract to mixed‐alcohols. Biofuel Bioprod Biorefin. 2018;12(6):1082-94. DOI |
10 | Fasahati P, Liu JJ. Application of MixAlco® processes for mixed alcohol production from brown algae: Economic, energy, and carbon footprint assessments. Fuel Process. Technol. 2016;144:262-73. DOI |
11 | Lonkar S, Fu Z, Wales M, Holtzapple M. Creating economic incentives for waste disposal in developing countries using the MixAlco process. Appl. Biochem. Biotechnol. 2017;181(1):294-308. DOI |
12 | Zhang F, Yu W, Liu W, Xu Z. The Mixed Fermentation Technology of Solid Wastes of Agricultural Biomass. Front. Energy Res. 2020;8:50. DOI |
13 | Agbogbo FK, Holtzapple MT. Fixed-bed fermentation of rice straw and chicken manure using a mixed culture of marine mesophilic microorganisms. Bioresour. Technol. 2007;98(8):1586-95. DOI |
14 | Pham V, Holtzapple M, El-Halwagi M. Techno-economic analysis of biomass to fuel conversion via the MixAlco process. J. Ind. Microbiol. Biotechnol. 2010;37(11):1157-68. DOI |
15 | Takaki M, Tan L, Murakami T, Tang YQ, Sun ZY, Morimura S, Kida K. Production of biofuels from sweet sorghum juice via ethanol–methane two-stage fermentation. Ind Crops Prod. 2015;63:329-36. DOI |
16 | Xiong Y, Zhang P, Luo J, Johnson S, Fang Z. Effect of processing on the phenolic contents, antioxidant activity and volatile compounds of sorghum grain tea. J. Cereal Sci. 2019;85:6-14. DOI |
17 | McGinnis MJ, Painter JE. Sorghum: History, Use, and Health Benefits. Nutrition Today. 2020;55(1):38-44. DOI |
18 | Thomas LL, Espinosa CD, Goodband RD, Stein HH, Tokach MD, Dritz SS, Woodworth JC, DeRouchey JM. Nutritional evaluation of different varieties of sorghum and the effects on nursery pig growth performance. J. Anim. Sci. 2020;98(5):120. DOI |
19 | Stamenković OS, Siliveru K, Veljko VB, Banković-Ilić IB, Tasić MB, Ciampitti IA, Đalović IG, Mitrović PM, Sikora VŠ, Prasad PV. Production of biofuels from sorghum. Renew. Sustain. Energ. Rev. 2020;124:109769. DOI |
20 | De Almeida LG, da Costa Parrella RA, Simeone ML, de Oliveira Ribeiro PC, dos Santos AS, da Costa AS, Guimarães AG, Schaffert RE. Composition and growth of sorghum biomass genotypes for ethanol production. Biomass Bioenergy. 2019;122:343-8. DOI |
21 | Vidut V, Grigore I Vladutiu L Udumitru D, Apostol, Parasciv G. Considerations concerning the valorization of the juice obtained from sugar sorghum from stalk from alcohol. Annals of the University of Craiova-Agriculture, Montanology, Cadastre Series. 2020;49(2):340-7. |
22 | Lau MH, Richardson JW, Outlaw JL, Fuller SW, Nixon CJ, Herbst BK. Location of a MixAlco Production Facility with Respect to Economic Viability. 2004. DOI |
23 | Zhang Y. Techno-economic and life cycle analysis of MixAlco® processes for mixed alcohol production from brown algae. Doctoral dissertation, Rutgers University-School of Graduate Studies. 2019. DOI |
24 | Fu Z, Holtzapple MT. Fermentation of sugarcane bagasse and chicken manure to calcium carboxylates under thermophilic conditions. Appl. biochem. biotechnol. 2010;162(2):561-78. DOI |
25 | Chan WN, Fu Z, Holtzapple MT. Co-digestion of swine manure and corn stover for bioenergy production in MixAlco™ consolidated bioprocessing. Biomass Bioenergy. 2011;35(10):4134-44. DOI |
26 | Black AS. The conversion of corn stover and pig manure to carboxylic acids with the MixAlco process. Doctoral dissertation, Texas A&M University. 2013. |
27 | Forrest AK, Hollister EB, Gentry TJ, Wilkinson HH, Holtzapple MT. Comparison of mixed-acid fermentations inoculated with six different mixed cultures. Bioresour. technol. 2012;118:343-9. DOI |
28 | Yadav KS, Naseeruddin S, Prashanthi GS, Sateesh L, Rao LV. Bioethanol fermentation of concentrated rice straw hydrolysate using co-culture of Saccharomyces cerevisiae and Pichia stipitis. Bioresour. technol. 2011;102(11):6473-8. DOI |
29 | Fu Z, Holtzapple MT. Consolidated bioprocessing of sugarcane bagasse and chicken manure to ammonium carboxylates by a mixed culture of marine microorganisms. Bioresour. technol. 2010;101(8):2825-36. DOI |
30 | Sluiter A, Hames B, Ruiz R, Scarlata C, Sluiter J, Templeton D, Crocker DL. Determination of structural carbohydrates and lignin in biomass. Laboratory analytical procedure. 2008;1617(1):1-6. |
31 | ASTM Standard. Standard Test Method Instrumental Determination.2003. |
32 | Adeyemi MM, Olatubosun RS, Babarinde OA, Omale PE. Comparative study of bioethanol production from wheat straw and rice straw. J. Chem. Soc. Nigeria. 2019;44(2). |
33 | Kshirsagar SD, Waghmare PR, Loni PC, Patil SA, Govindwar SP. Dilute acid pretreatment of rice straw, structural characterization and optimization of enzymatic hydrolysis conditions by response surface methodology. RSC Adv. 2015;5(58):46525-33. DOI |
34 | Gely MC, Pagano AM. Effect of moisture content on engineering properties of sorghum grains. Agric. Eng. Int. CIGR J. 2017;19(2):200-9. |
35 | Peiris KH, Bean SR, Chiluwal A, Perumal R, Jagadish SK. Moisture effects on robustness of sorghum grain protein near‐infrared spectroscopy calibration. Cereal Chem. 2019;96(4):678-88. DOI |
36 | Berbert PA, Moura EE, Molina MA, Soares KJ, Oliveira MT. Density-independent radiofrequency dielectric models for moisture estimation in grain sorghum. J. Food Meas. Charact. 2017;11(1):204-12. DOI |
37 | Raihanatu MB, Modu S, Falmata AS, Shettima YA, Heman M. Effect of processing (sprouting and fermentation) of five local varieties of sorghum on some biochemical parameters. Biokemistri. 2011;23(2). |
38 | Christakopoulos P, Li LW, Kekos D, Macris BJ. Direct conversion of sorghum carbohydrates to ethanol by a mixed microbial culture. Bioresour. technol. 1993;45(2):89-92. DOI |
39 | Gregg DJ, Saddler JN. Factors affecting cellulose hydrolysis and the potential of enzyme recycle to enhance the efficiency of an integrated wood to ethanol process. Biotechnol. Bioeng. 1996;51(4):375-83. DOI |
40 | Dessì P, Sánchez C, Mills S, Cocco FG, Isipato M, Ijaz UZ, Collins G, Lens PN. Carboxylic acids production and electrosynthetic microbial community evolution under different CO2 feeding regimens. Bioelectrochemistry. 2021;137:107686. DOI |
Cite this article:
Shalsh, F., Abdul Alrazzaq, N., Nagimm, D., Abdul Alrheem, M., Abedul Alrheem, S., Abd alalah, K. Bioconversion of white sorghum biomass using MixAlco fermentation process. DYSONA – Applied Science, 2021;2(1): 21-27. doi: 10.30493/das.2021.248966